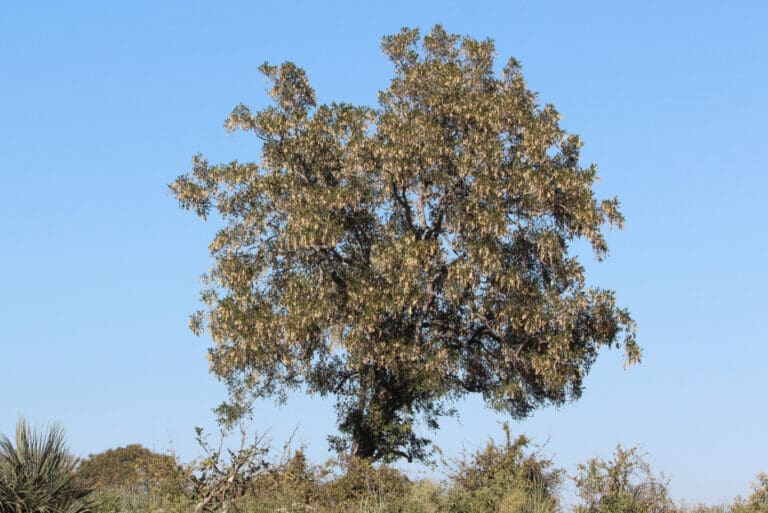
African Blackwood
The life of an oboe begins 200 years before a Howarth craftsman starts their work. This is the time it takes for an African Blackwood tree (Dalbergia melanoxylon) to mature to a harvestable size. We mostly use African Blackwood for our oboes. It is supplied to us as square blocks (billets) from Tanzania and Mozambique in East Africa. We also use Cocobolo wood (Dalbergia retusa) which is red/orange in colour and grows in South America.
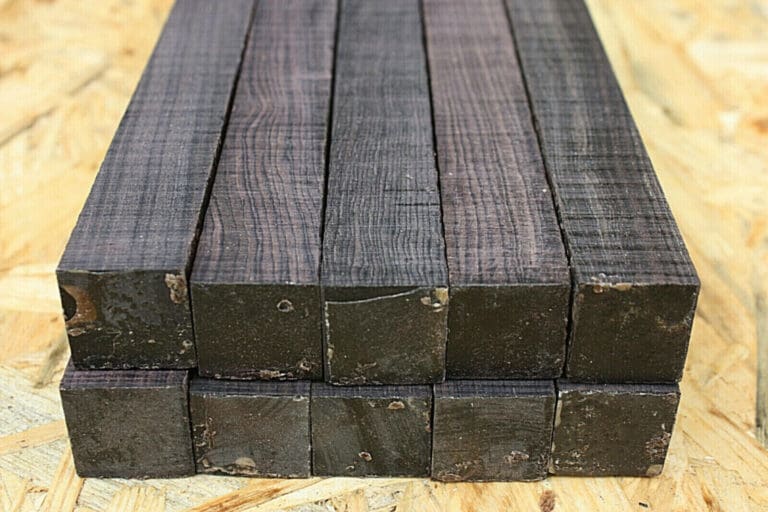
We receive billets of wood
It takes approximately ten hours spread over several years to turn the square blocks of wood into the three wooden parts that make up the body of the oboe. The square billets of Blackwood have now been rough turned and drilled with a pilot hole. These are then stored for several years to season.
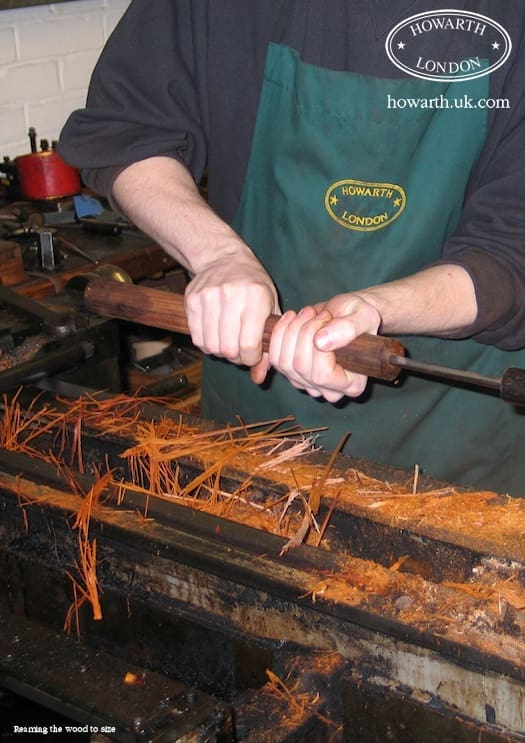
We turn the billets
We work the billets to their final shape through different stages allowing the wood to rest in between. After we have turned the blocks into a round shape and drilled a pilot hole up the middle of the wood we form the bored hole into a conical shape with a tool called a reamer. We add a metal socket that will hold the reed and then turn the external profile.
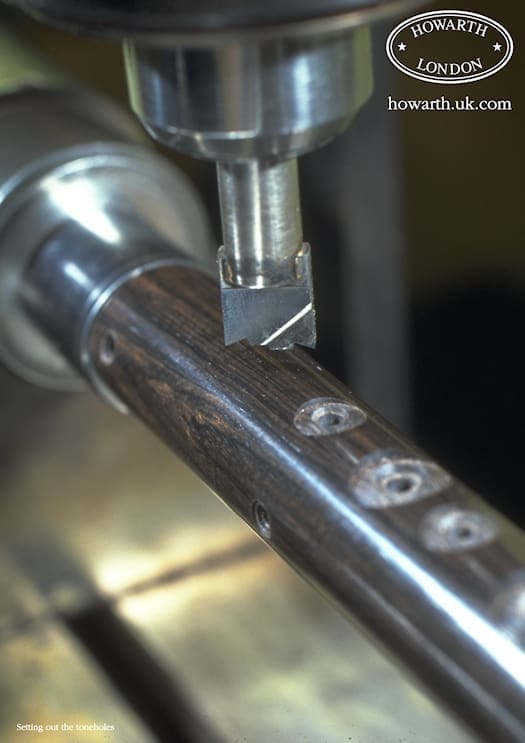
The body and all metal components for the mechanism are made on a CNC mill
Once the wooden pieces have been machined, the three wooden parts of the oboe are selected and matched together. We machine the end of each joint so that each of the pieces fit together. They will stay together now for the life of the oboe. We design the size and layout of the holes that produce the different notes. These precise measurements are then loaded on to a computer. We use a computer-controlled milling machine to drill the holes and any clearances required to accommodate the keywork.
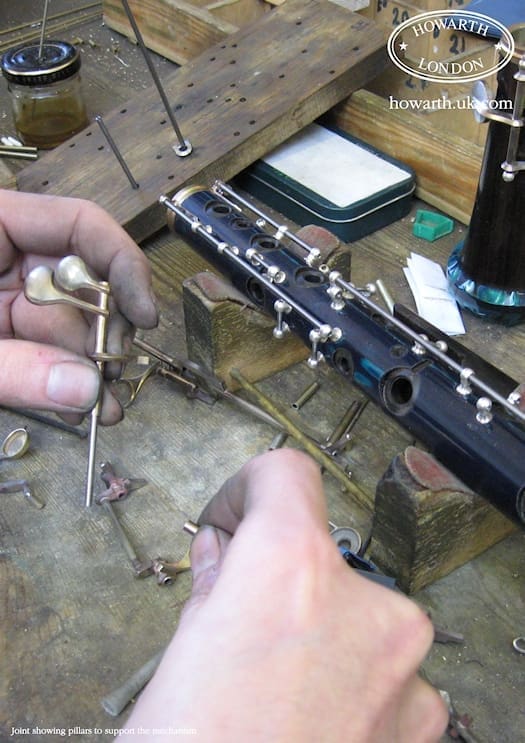
The keys are made
The instrument’s keys are all hand-made. This can take between 20 and 60 hours to complete depending on the model. We screw small posts in to the threaded holes in the wooden body. We line these up accurately by hand and then drill them to add a steel axle rod on which the individual keys move. Many posts have a small holed drilled through the stem to anchor a spring used to activate the mechanism. These tiny holes are less than half a millimetre in diameter and are drilled freehand!
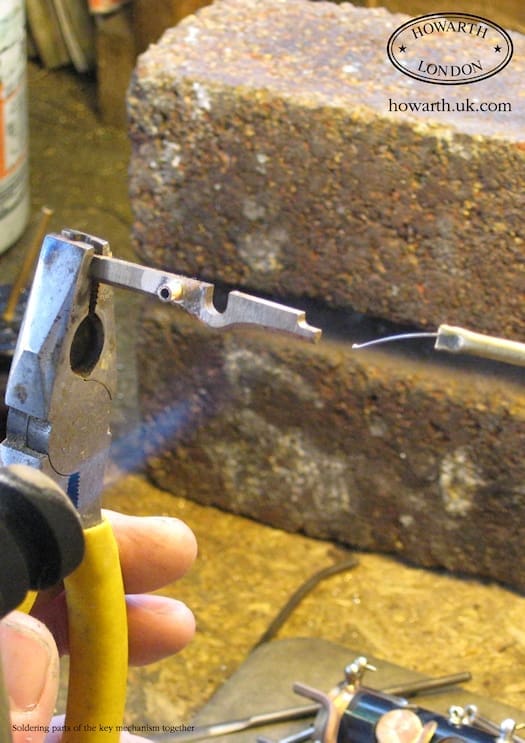
The keys are fitted
The keys are hand-fitted to each instrument to ensure they fit precisely between the pillars. We work with up to 200 metal components when assembling the keywork. These pieces are silver-soldered together. We make these components from tiny pieces of nickel silver. We design each mechanical part and then machine them to our own specifications. Many of the keys are finished with a bevelled edge. We machine these edges by hand on the individual key parts. We then fit every oboe key to the instrument by hand and then test the mechanism.
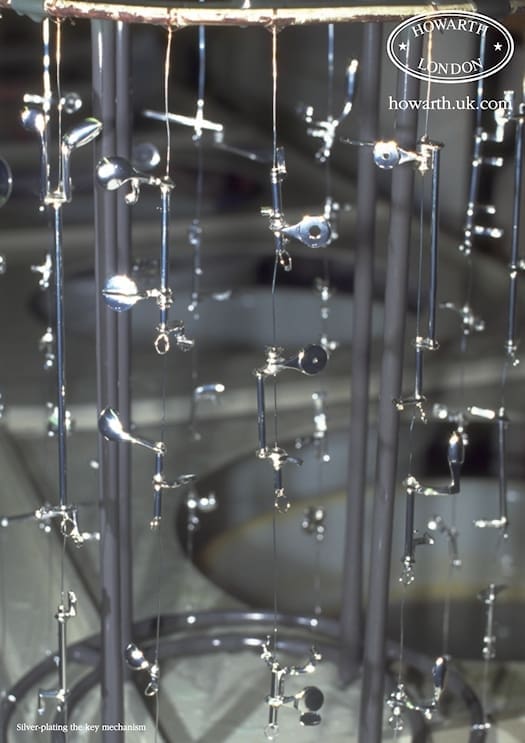
The keys are plated
Once we have built the mechanism, we take all the keys off the instrument and polish them until we achieve a perfectly smooth surface. We then give each of the keys a generous layer of silver plating. The overall dimensions of each key increases by the amount of silver deposited in the plating process. We have to remove this deposit from the inside and from the ends of each key to regain the original dimensions of the key.
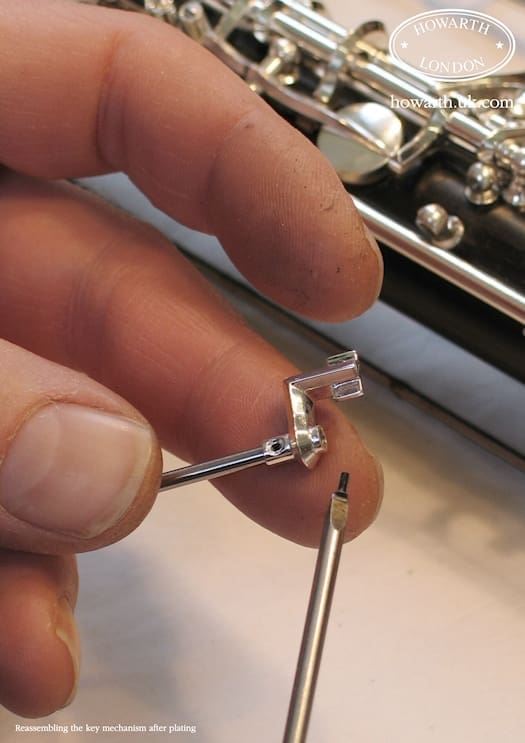
The instrument is ready for final assembly
We now re-assemble the oboe for the last time. We reposition the keys between the posts of the instrument and carefully test to ensure there is a small amount of space to let the keys move. It takes up to 76 tiny screws to assemble an oboe, depending on the model. These hold the keys in place and are used to make fine adjustments to the instrument. We glue on pieces of thin cork sheet to cushion the keys and the wooden body at each contact point on the instrument.
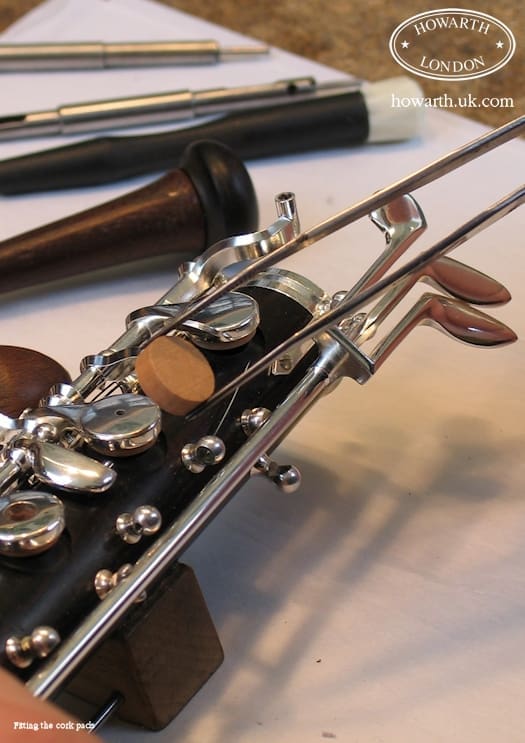
The instrument is padded
We add cork and leather pads to ensure an airtight seal over each of the tone holes. Each pad is carefully adjusted so it fits perfectly into the keys. We gently heat each key and add a small amount of glue to hold the pad in place. The face of each cork pad is carefully sanded to make sure that it fits perfectly against the finely cut rim of the tone-hole. We glue cork to the joints to make an airtight sliding fit between the three parts of the body.
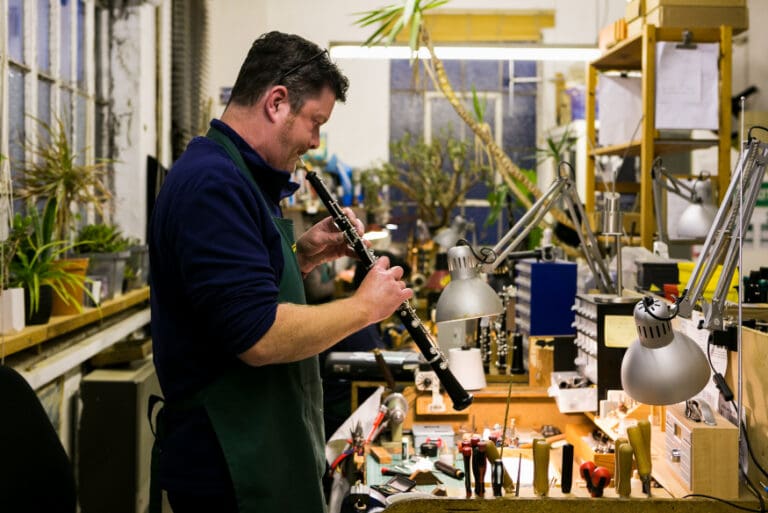
The instrument is ready for testing
The instrument is now ready to produce its first musical sounds. We make tiny adjustments to ensure evenness of tone and tuning, and the necessary mechanical precision. Only then is the instrument ready to be played and enjoyed by the musician. In all, six technicians will have spent upwards of 80 hours working with over 200 components in total to make what is accepted as one of the finest oboes in the world.